31/01/2024
Sabancı University and Tusaş Engine Industries (TEI) have collaborated on a project that will contribute to the aviation industry. The project, titled "Cutting Optimization with Water Jet," aims to contribute to the transformation of the production processes of Inconel integrally bladed turbine disks, i.e. BLISKS, which are crucial components of turbofan jet engines that enable the flight of passenger aircrafts such as Airbus A320neo and Boeing 737 MAX type. This collaboration seeks to achieve sustainable and environmentally friendly production technologies in the aviation sector, leading to lower investment and operational costs, while also enabling high-profit material recycling.
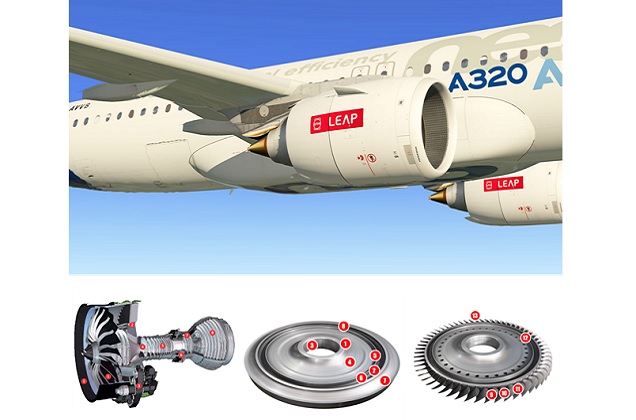
(a) Turbofan Jet Engine, (b) Integrally bladed disk (BLISK), raw material and final part geometry
Source: https://xplanereviews.com/index.php?/forums/topic/693-news-airbus-a320-251n-leap-by-peters-aircraft/
Source: https://www.iscar.com/newarticles.aspx/lang/en/newarticleid/1398
Within the scope of the project, the goal is to replace the high cost rough milling stage in the machining of BLISKS in turbofan jet engines, which are the main power source for passenger aircrafts to fly. This transformation aims to replace the traditional machining methods, particularly rough milling, with abrasive water jet machining technology. This development presents an opportunity to implement a completely innovative production approach when compared to long-standing manufacturing methods.
The target parts pose various challenges in conventional machining due to being designed from Inconel (Nickel alloy), one of the most difficult-to-cut metals, and having generally complex surface geometries, especially in the case of BLISKS. In this study, calculation of geometrically suitable flow paths and the selection of process parameters will be carried out to enable the production of the relevant parts with 5-axis abrasive water jet machining. Ultimately, the aim is to demonstrate the feasibility of this concept and the potential cost savings that can be achieved on the selected two real application parts.
In this project, Sabancı University will develop the 5-axis abrasive water jet rough machining process and will conduct the concept design. In this regard, tasks will include the selection of process parameters, verification of geometric suitability and repeatability, application on full-scale parts, and experimental investigation of the effects on the semi-finish milling stage after abrasive water jet rough cutting. As a result, while production costs are significantly reduced, energy savings will be achieved, and the residue material will be recycled at the maximum possible monetary value compared to the conventional forms of metal chips.
The project will be coordinated by Lütfi Taner Tunç and Erhan Budak, faculty member at the Faculty of Engineering and Natural Sciences. In areas such as intellectual property rights and stakeholder access, support will be provided by Can Kartoğlu, the Project Partners Manager of the Research Development and Technology Transfer Office (SUATT), and Cem Emre Memiş, the External Stakeholder Access Manager. The cutting infrastructure at SU-IMC for water jet cutting applications will be procured for the project, and semi-precision milling, surface, and geometric analyses on the parts will be carried out at the Manufacturing Research Laboratory located at Sabancı University Tuzla Campus.
Successful completion of this process concept will enable a significant reduction in costs through a completely new approach in the production of Inconel-type turbine components in the aviation sector. This transformation will enable manufacturing in aviation to be more environmentally friendly, sustainable, and profitable for material recycling. Additionally, it is expected that the project will have a transformative impact on jet engine production technologies in Turkey, particularly increasing independency in developing domestic manufacturing technologies, overcoming the bottleneck of expensive and precise manufacturing machinery in critical areas, and reducing initial investment costs. Furthermore, the outputs of this project have the potential to create similar impacts and transformation in several other industries.